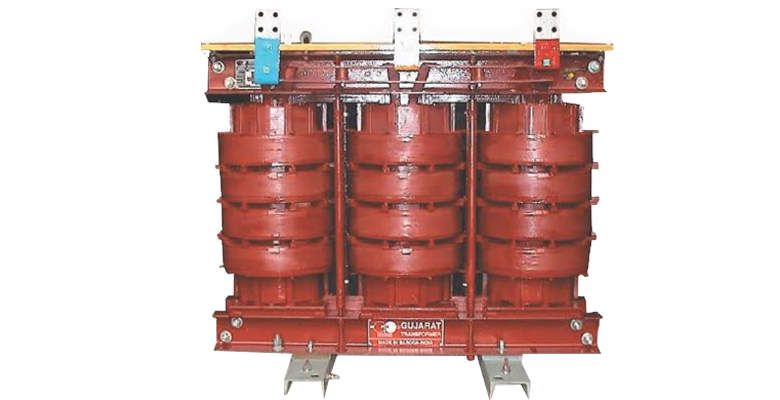
The dry-type resin dipped transformers differ from the oil type because of their HV winding coating, made in epoxy resin under vacuum. Such transformers are made under natural fan-cooled or air-cooled options with varied power ranges and voltage levels.
Originating in the city of Vadodara from Gujarat, these transformers were designed to meet the requirements of advanced tech and power output incorporation in their designs. Currently, these transformers are produced with less environmental risks, low maintenance, and moisture resistance. Here’s more about them:
Epoxy resin
Epoxy resin is used for fireproofing or insulating a substance as a raw material component in electrical products. It doesn’t deform after molding and maintains its finish in dusty or humid environments.
The dry stages of epoxy resin casting are called B grade, which eventually reach F and H grades with higher insulation.
Characteristics
These are the characteristics of dry type resin dipped transformer:
- High dielectric strength – the dielectric breakdown field strength of this transformer ranges from 18 to 22k V/mm
- Short circuit resistance is rarely damaged because of their integral casting, curing, and heating, which increases their mechanical strength.
- Disaster prevention –comes with flame retardance and can extinguish itself quickly.
- Harsh environments work well under humidity, atmospheric pollution, and dust.
- Maintenance workload – Low temperature and humidity control load display, reducing operational costs.
- Efficiency is built with high operating efficiency, low noise and loss, easy installation, and compact design.
Design
This is the design of the dry type resin dipped transformer:
- The core is made in silicon steel sheet to improve permeability and reduce eddy current loss.
- Winding – is determined by the magnetic flux density, which is inversely proportional to the winding. Load loss, load current, and impeding voltages play a part in the flux density.
- Winding arrangement – this arrangement distinguishes transformers from the other types.
- Voltage coil – an air duct is placed between the windings to ensure inter-layer voltages.
- Wire–wound structures are cylindrical to fit the flat copper wires, along with a foil to ensure resistance and production efficiency.
- Short circuit impedance – core diameter is reduced by increasing the winding to maintain the impedance.
- No-load – the load characteristic determines the core structure of the transformer.
- Load loss is determined by the resistance loss in the transformer with the changes made to the low and high-voltage coils.
Conclusion
In conclusion, the dry-type resin-dipped transformer is a savior to ensure good distribution in high-moisture and chemical exposure areas. They are versatile with low maintenance. Since the coverage is continual, they are safe and proofed. The insulation is top tier, and the design works adequately under harsh environments. With the right manufacturers, the short circuit resistance and high dielectric strength can be an added benefit for many.